Mechanical / Hardware Design Projects
YKK Fenestration Actuators
Spring 2020 to Present
Further descriptions and updates coming soon.

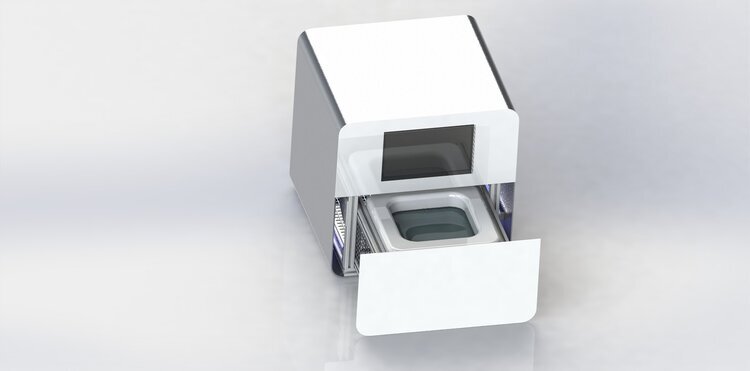


COVID Killer: Retail Sanitization Machine
Fall 2020
Further descriptions and updates coming soon.
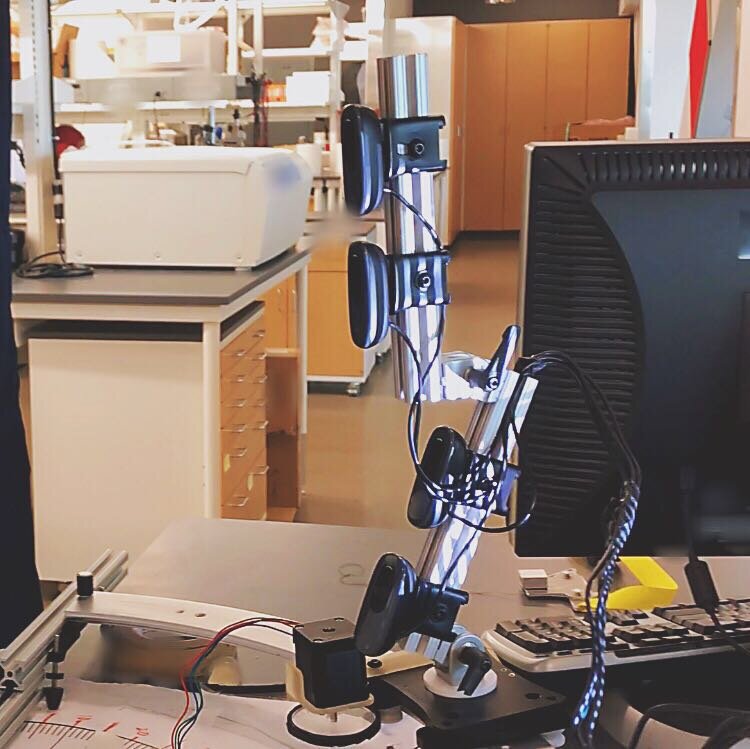

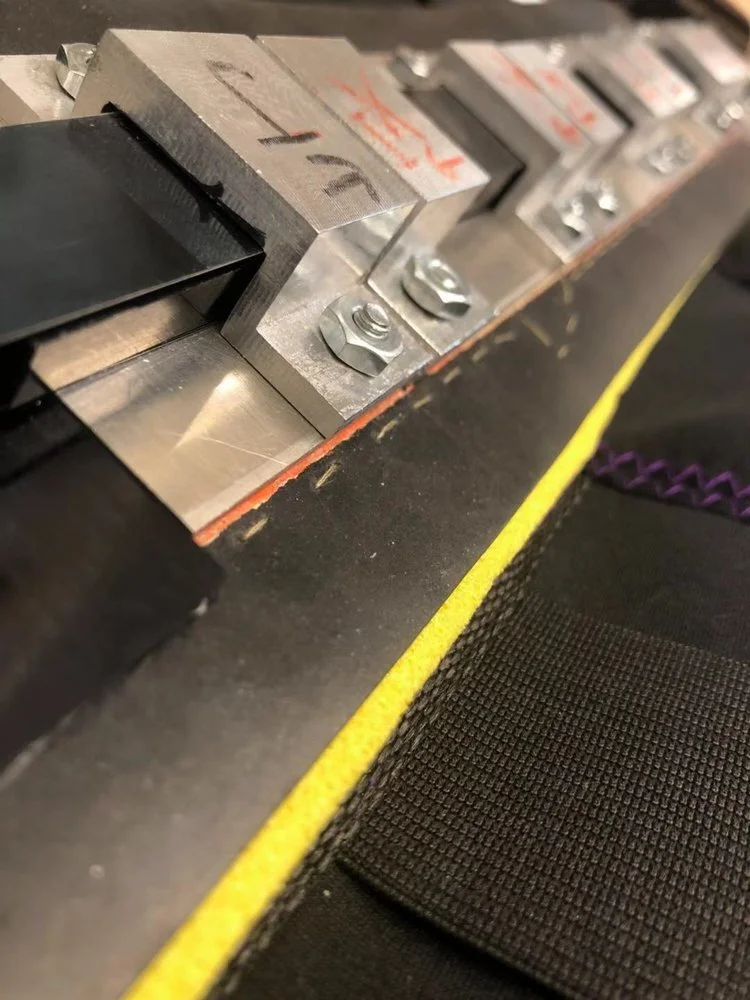

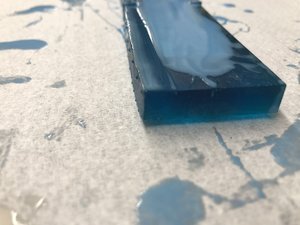

Bipap Mask Customization & Exoskeleton Spine Brace
Spring 2018 to Fall 2019
The mask customization research project as a whole was to figure out a better solution to customize BiPAP masks for ALS patients so that they can breathe in comfort during sleep. The whole customization process includes face contour scanning, 3D printing interface and silicone molding. My job was to develop a micro-stepping control feature and a driving mechanism to better control the scanner to optimize mesh outputs of face contours.
Skills practiced: Python 2.7 (openCV, pySerial), Arduino, C++, Meshlab, Laser Cutting, Silicone Molding
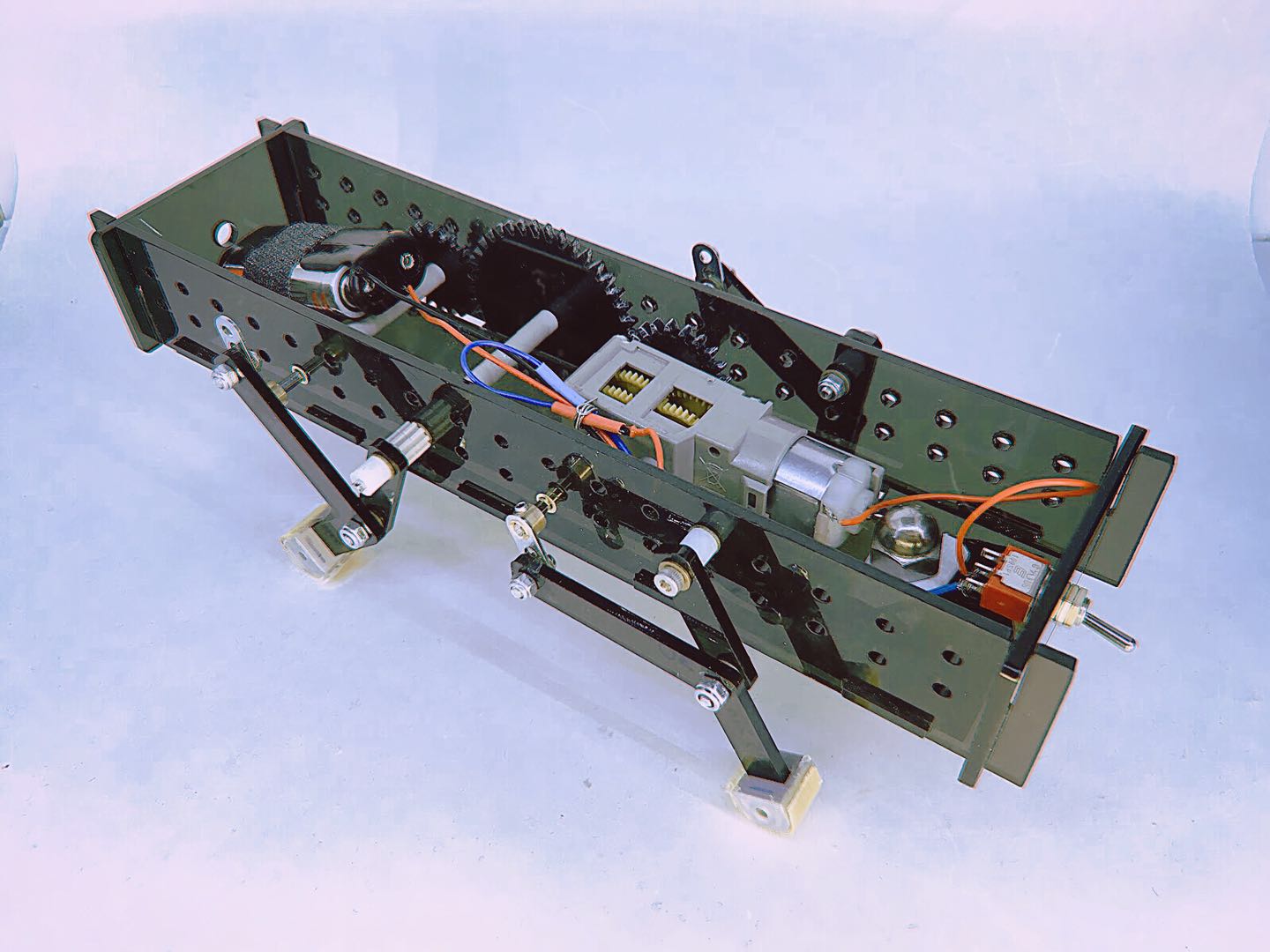
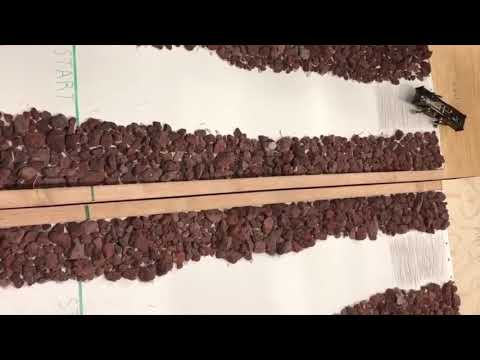
The Walking Robot
Fall 2018
The walking robot is a course project of CMU Engineering Design I. In team of four, we were required to design a sensorless 4 legged robot to cover two different gentle hills terrains with 1 adjusting touch on each. During the project I learned how to generate coupler curves and retrieve linkage data for legged robots. We finished our robot one day earlier to participate in early testing and it was the only robot that successfully completed both courses.
Skills practiced: Motion Analysis, Problem Solving, Teamwork, SolidWorks (assembly, equations), 3D Printing (Ultimaker), Soldering, 4-bar Linkage Design
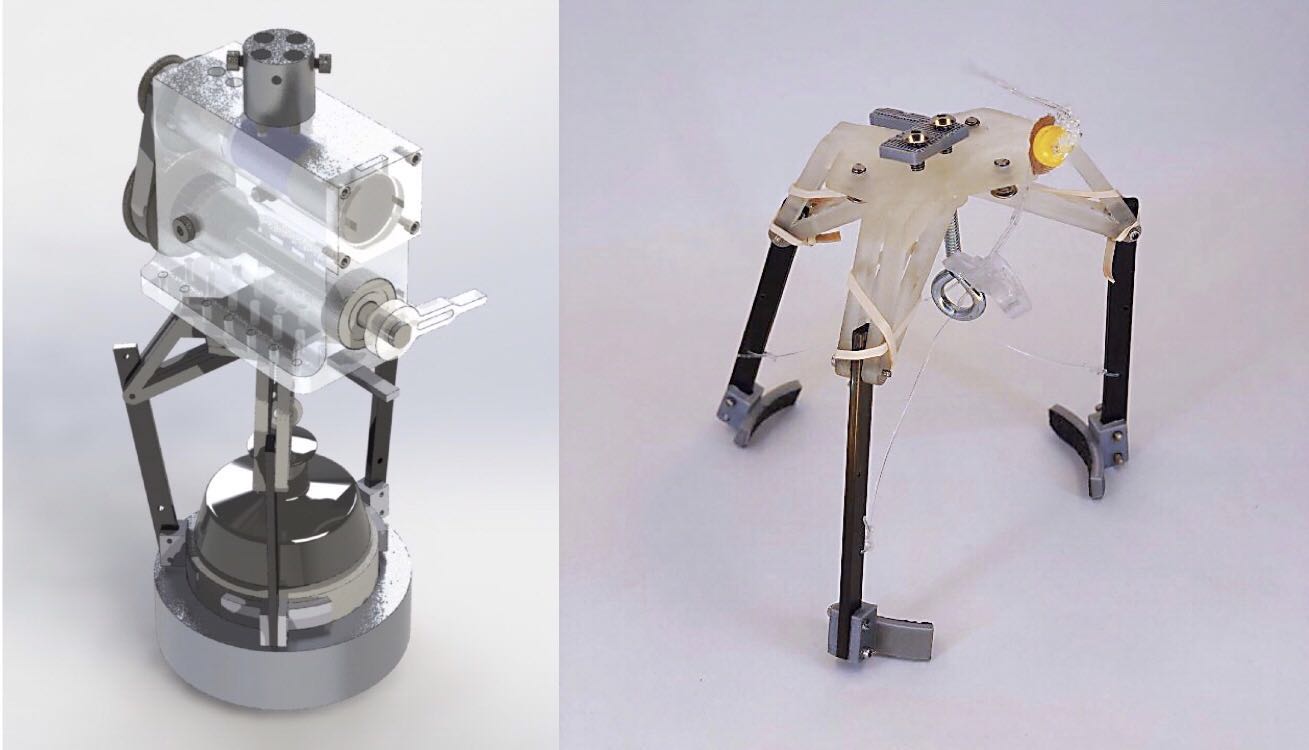
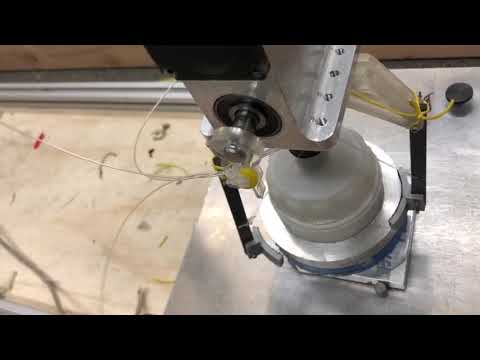
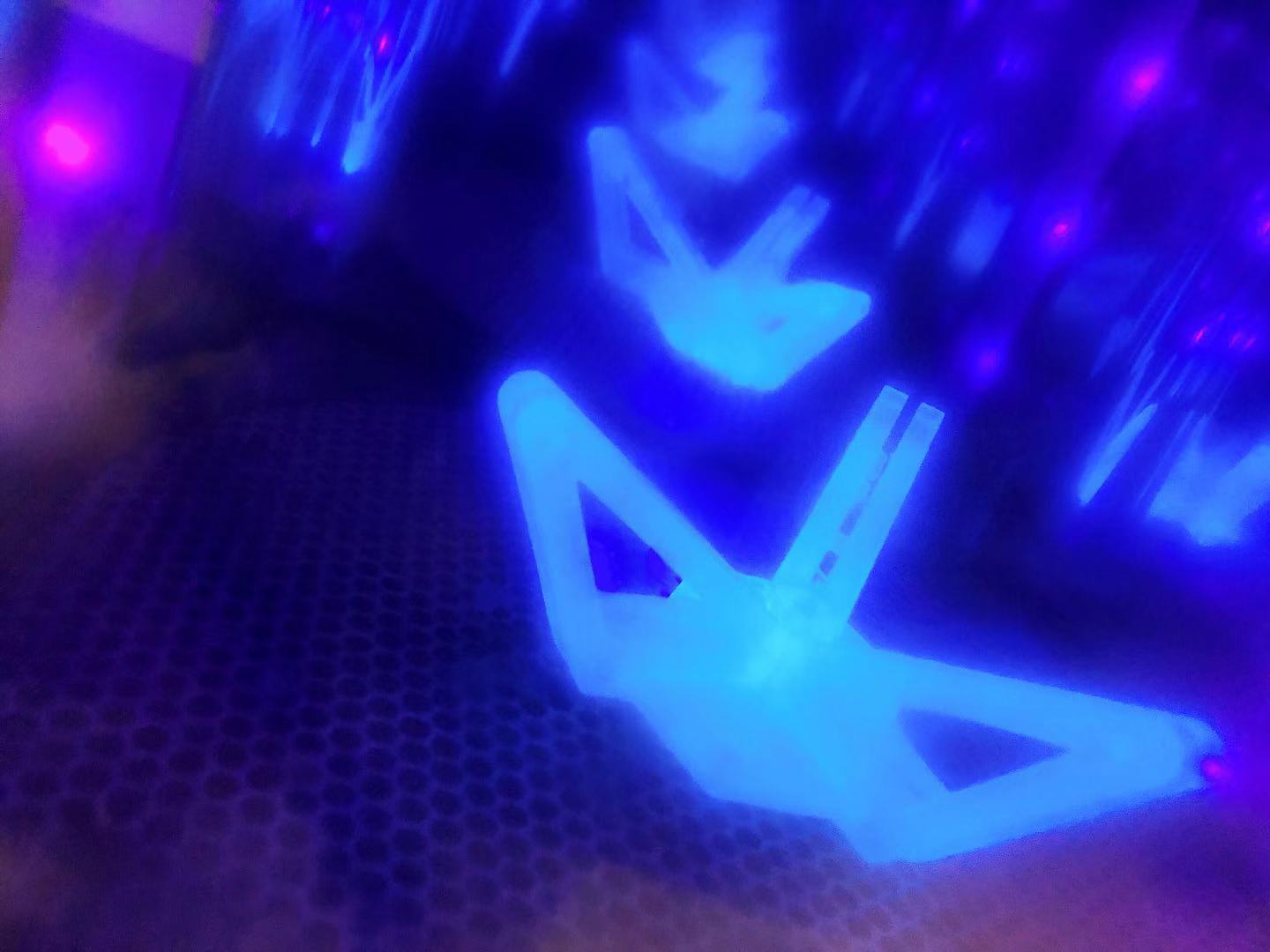
The Swinging Gripper
Fall 2018
The Gripper is a team project of Engineering Design I, where the challenge was to create a lightest mechanical gripper design to pick up and release a 829-gram-artifact (water bottle) within budget and size constraints. The gripper design should be able to hold the object firmly during a circular swinging motion of a robot arm, where the slipping tolerance was 0.1inches. During the project, I was responsible for the gripping mechanism analysis, spool design, prototyping and the final revision of our design. The project nourished my knowledge of trade-offs between various material (ABS, PLA, PMMA, CF). Our gripper design successfully passed final tests and weighed only 83.6 grams.
Skills practiced: Material Analysis, Motion Analysis, Problem Solving, Teamwork, SolidWorks (assembly, motion study), 3D Printing (Form 2, Ultimaker, NVBot)
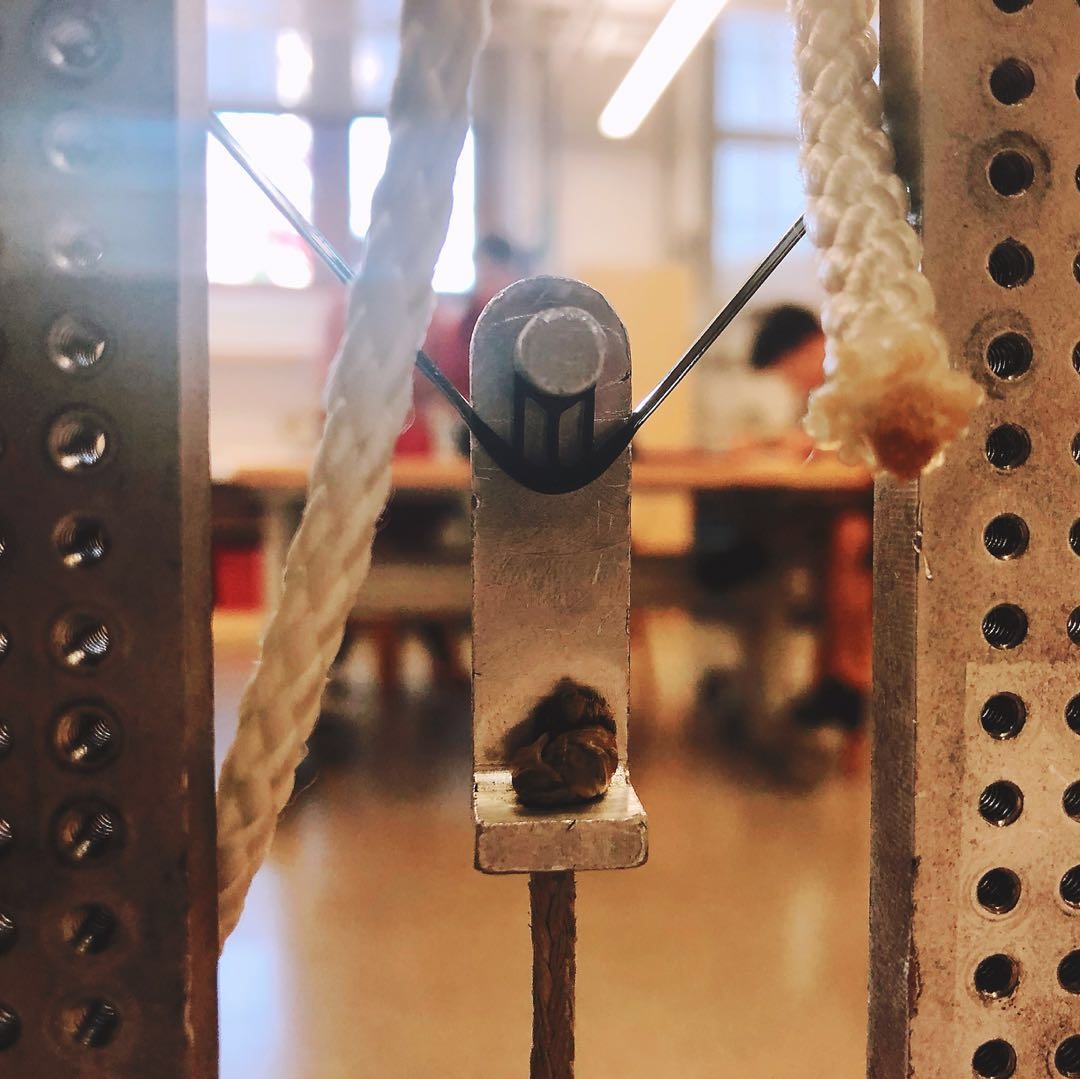
The Astronaut’s Coat Rack
Fall 2018
Coat rack design was the first course project of Engineering Design I. We were asked to create a coat rack design using least acrylic material with constraints on manufacturing quality, attachment region and clip position to hold a 25 lbf load (11.34 kg). There were forbidden areas where the bracket cannot cover and strict requirements for the clipping position, so I had to raise the clip using a double parallelogram structure while taking the advantage of its deformation. My design weighed 0.79 grams, among top 3% in class.
Skills practiced: Stress Analysis, SolidWorks(FEA, sketching, engineering drawing), Laser Cutting

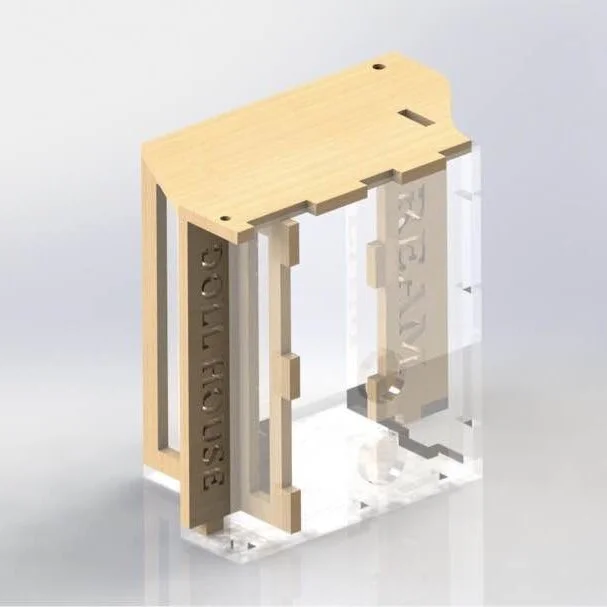
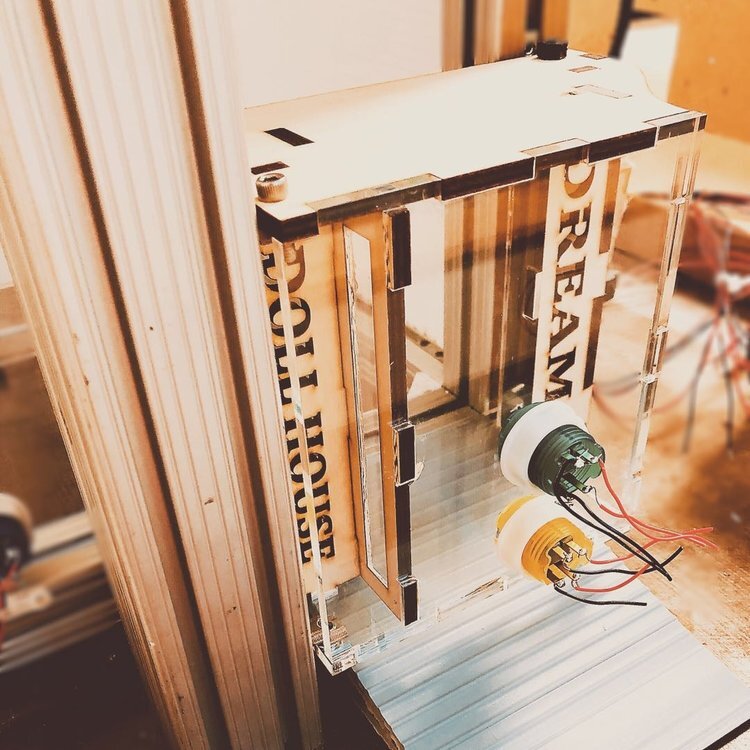
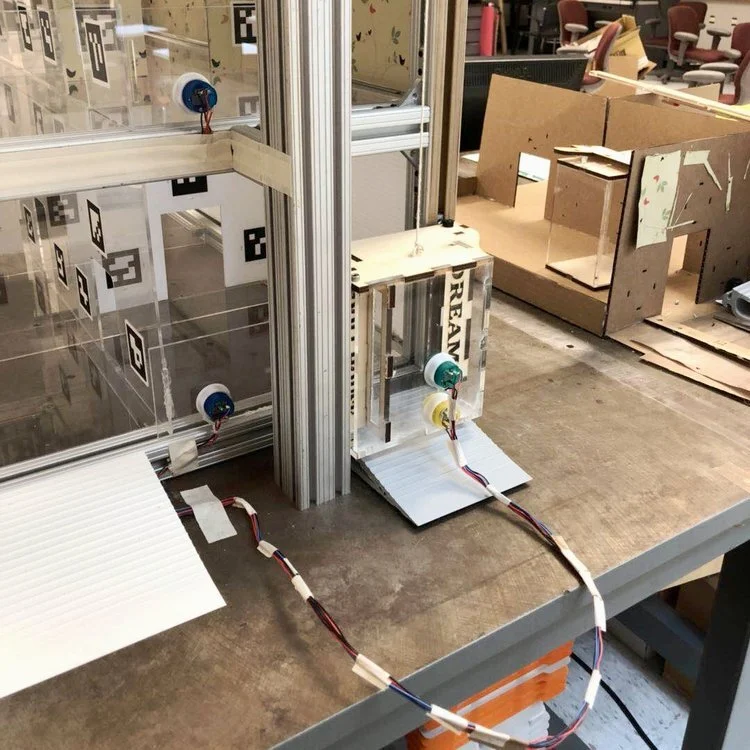
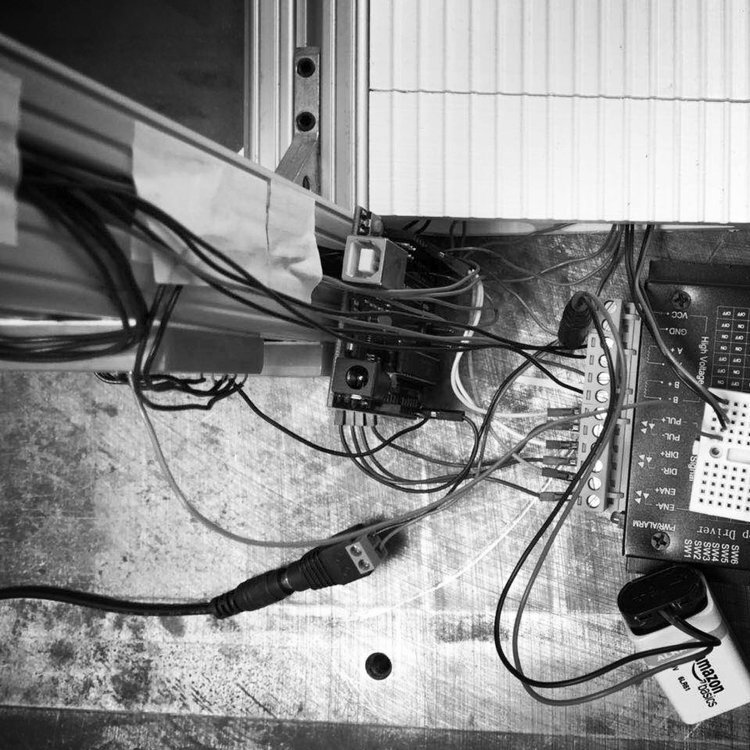
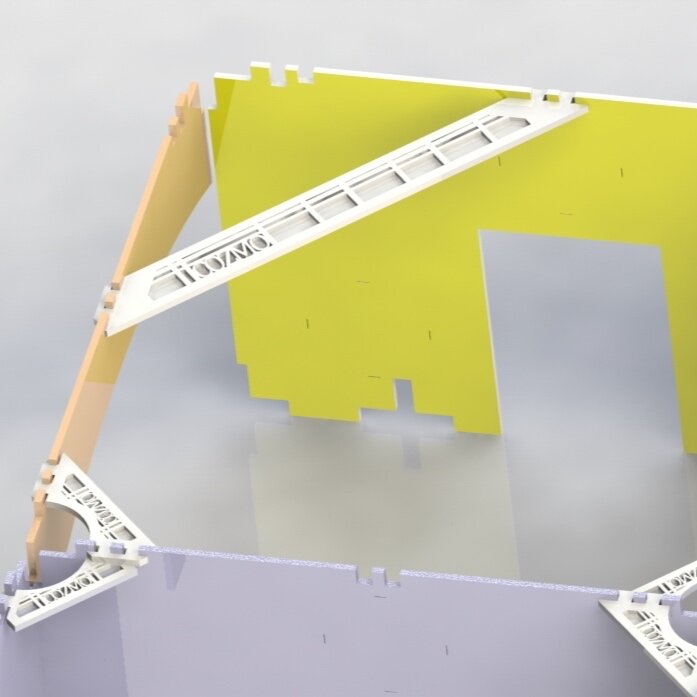
Anki Cozmo’s Elevator
Summer 2018
This is a mini elevator which I designed, fabricated and programmed to support a cognitive robotics course. The goal was to build an elevator which can be called by buttons with time delay sensing and carry a Cozmo robot up and downstairs in a 3-stories robot house.
Skills practiced: Rapid Prototyping, SolidWorks (sketching, engineering drawing, assembly), Laser Cutting, Arduino, Bipolar Stepper Motor (micro-step driver), Milling, Soldering, 3D Printing (Ultimaker)
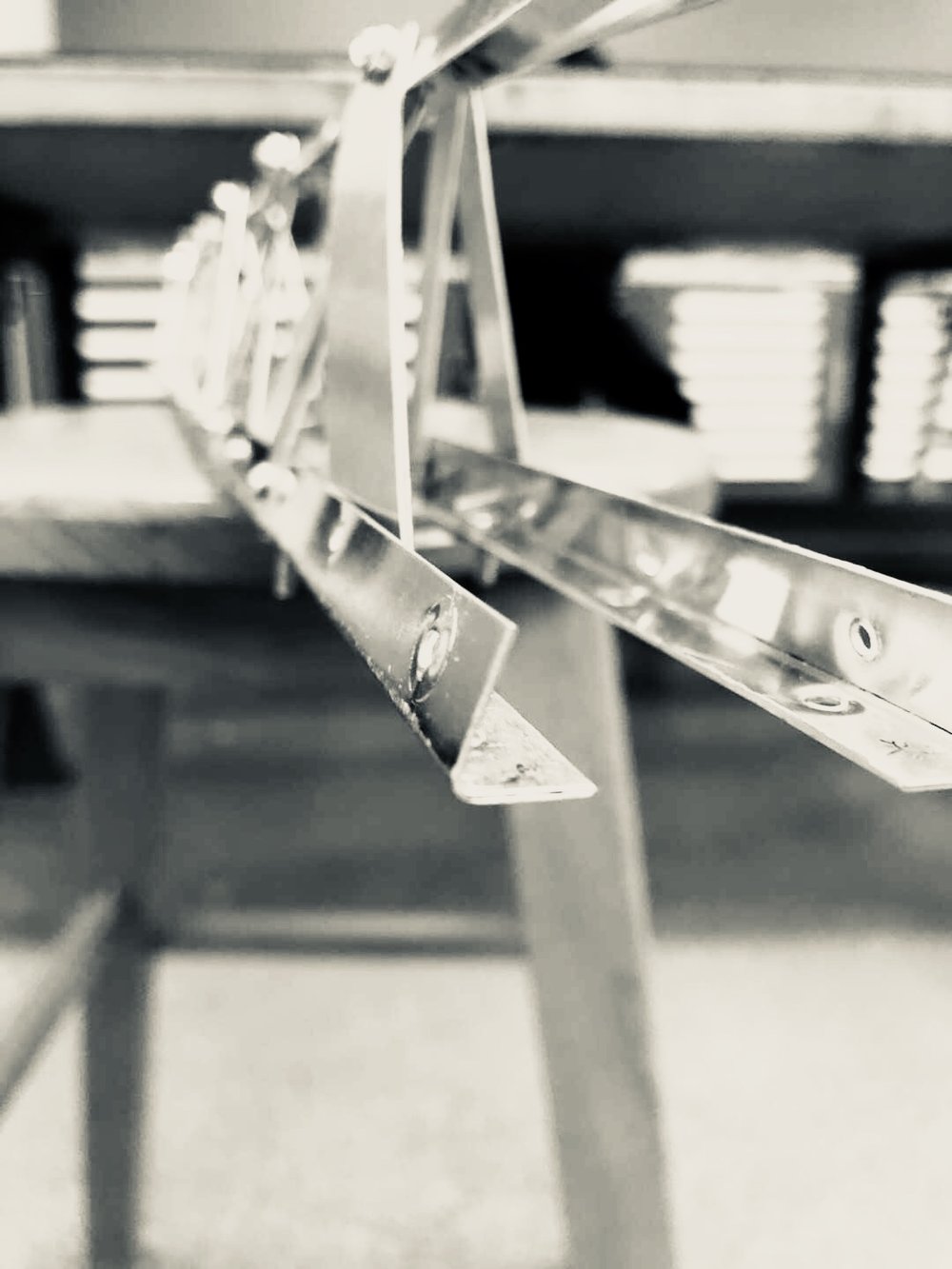
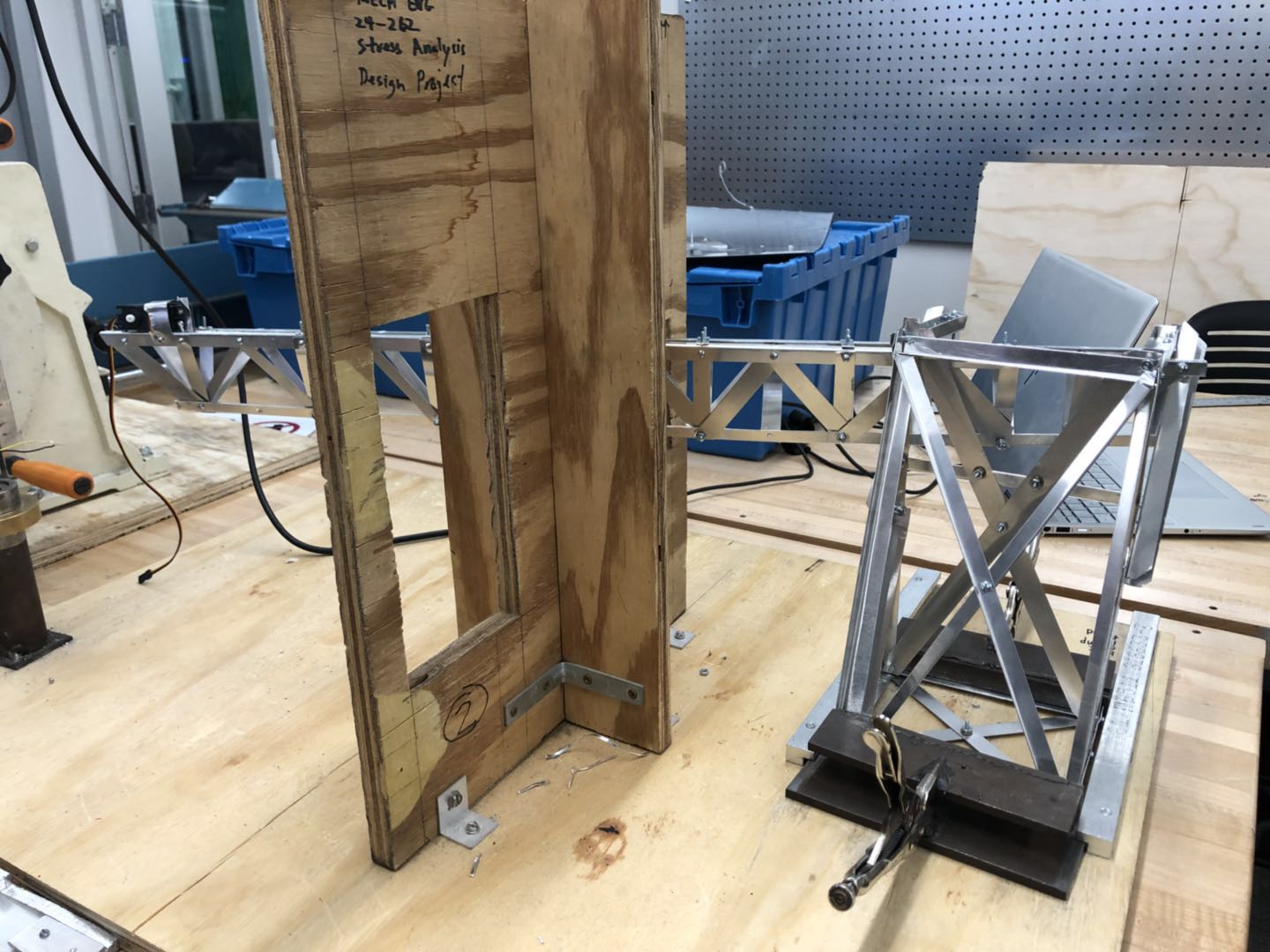
Mechanical Crane
Spring 2018
The term project of Stress Analysis was a task to design a mechanical crane in a team of 3, where I was responsible for base design and structural analysis. The requirement was to design and build a crane less than 20 ounces and lift a 2 pounds load up to 2 inches high using a 75 inch-ounce motor. During the project we gained a lot of hands-on experience with structural design and aluminum bending. Our crane managed to lift the object to 4.1 inches, which was more than twice of the requirement.
Skills practiced: Stress Analysis, Failure Analysis

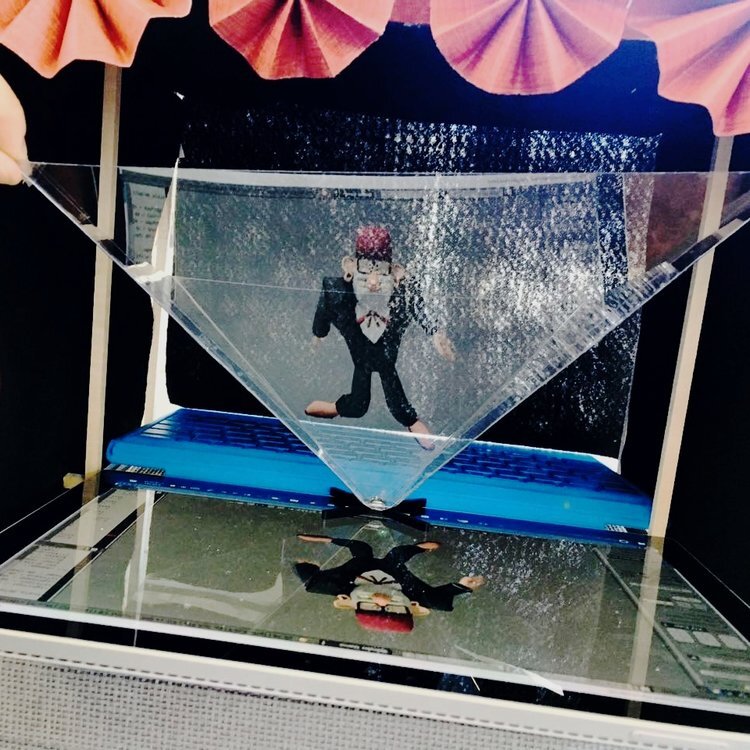
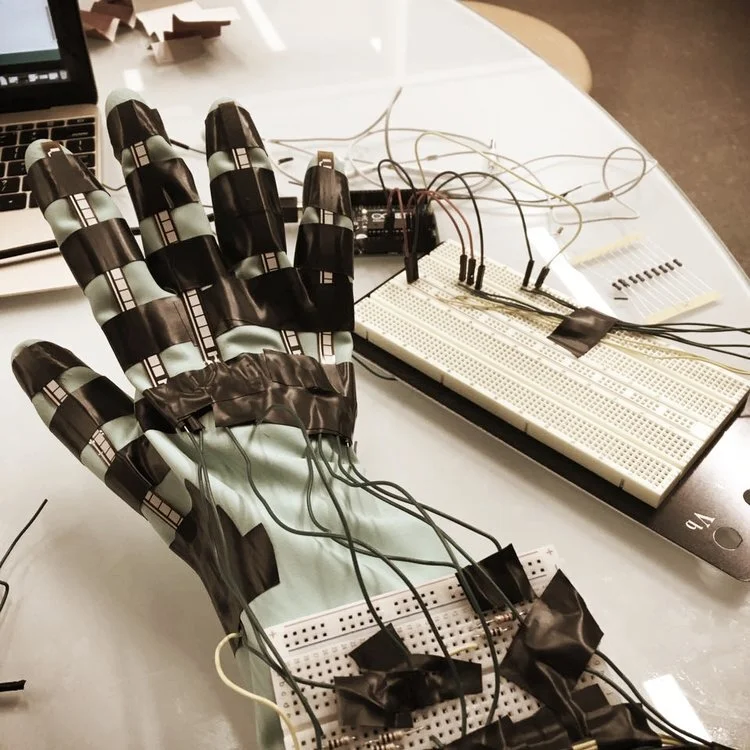
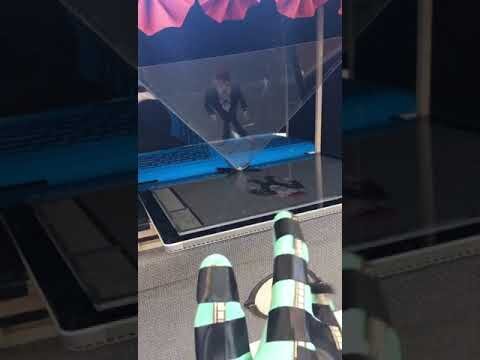
A Doll’s Glove: Sensor Driven Virtual Puppet
Spring 2018
During the Build 18 hardware hackathon of 2018, our team created a virtual hand puppet so that our users can control a virtual puppet using a flex sensor glove. Multiple flex sensors were applied to detect real-time data and transfer these data into blender to create movements on a virtual skeleton. The project won the Media Magician prize for best documentation and presentation.

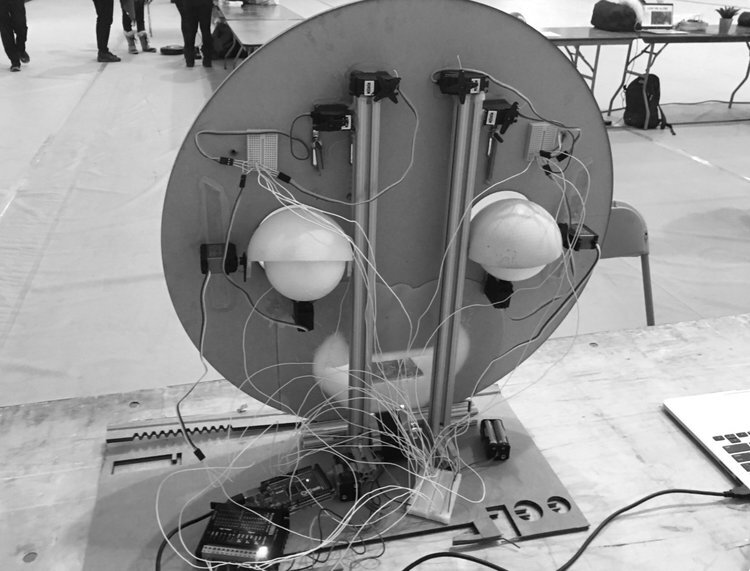

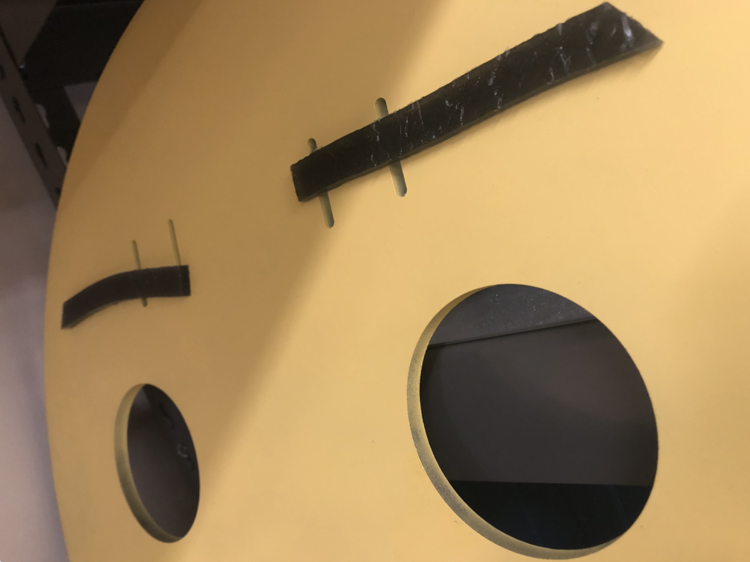
A Giant Emoji: A Facial Expression Mimicking Robot
Spring 2019
A Giant Emoji is a build 18 project for fun. It tracks landscape points in facial expressions and mimic those expressions through controls of servos and spring systems. Before everything started our friends were teasing that it would seem as useful as a 5 dollar toy, but the joy and fun it brought during the showcase session was definitely much more than that.
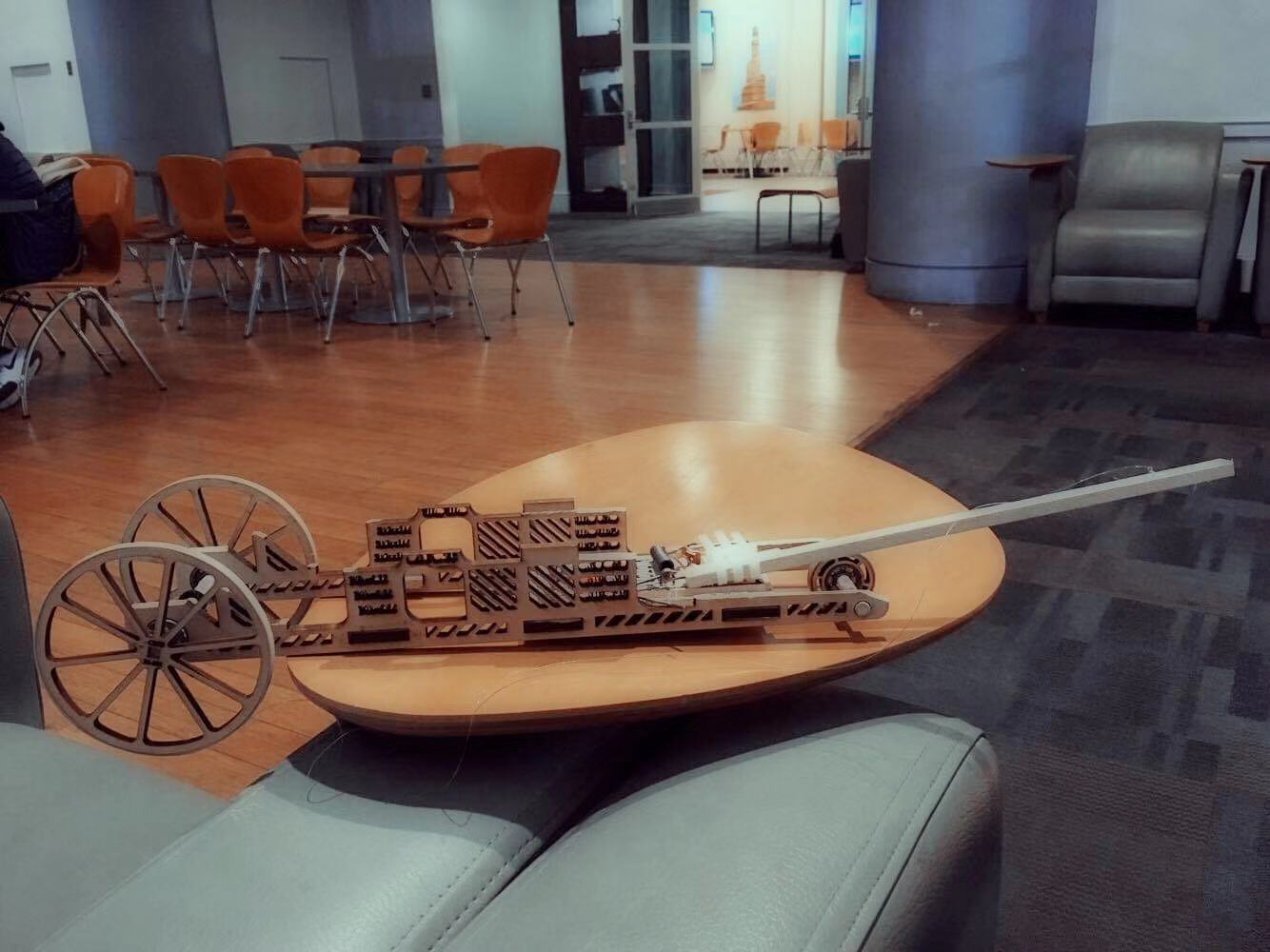
Mousetrap Car
Fall 2016
This is the first hands-on experience I had at CMU. We were asked to build a fastest mousetrap vehicle which could move back and forth 17 feet using whatever technology we have learned. I designed the vehicle using Creo Pro/E and made the prototypes through laser cutting. My most utilitarian design ever. It was the fastest and most consistent design in the final competition.
Skills practiced: Motion Analysis, Creo Pro/E (sketching), Laser Cutting, 3D Printing (Cube Pro)